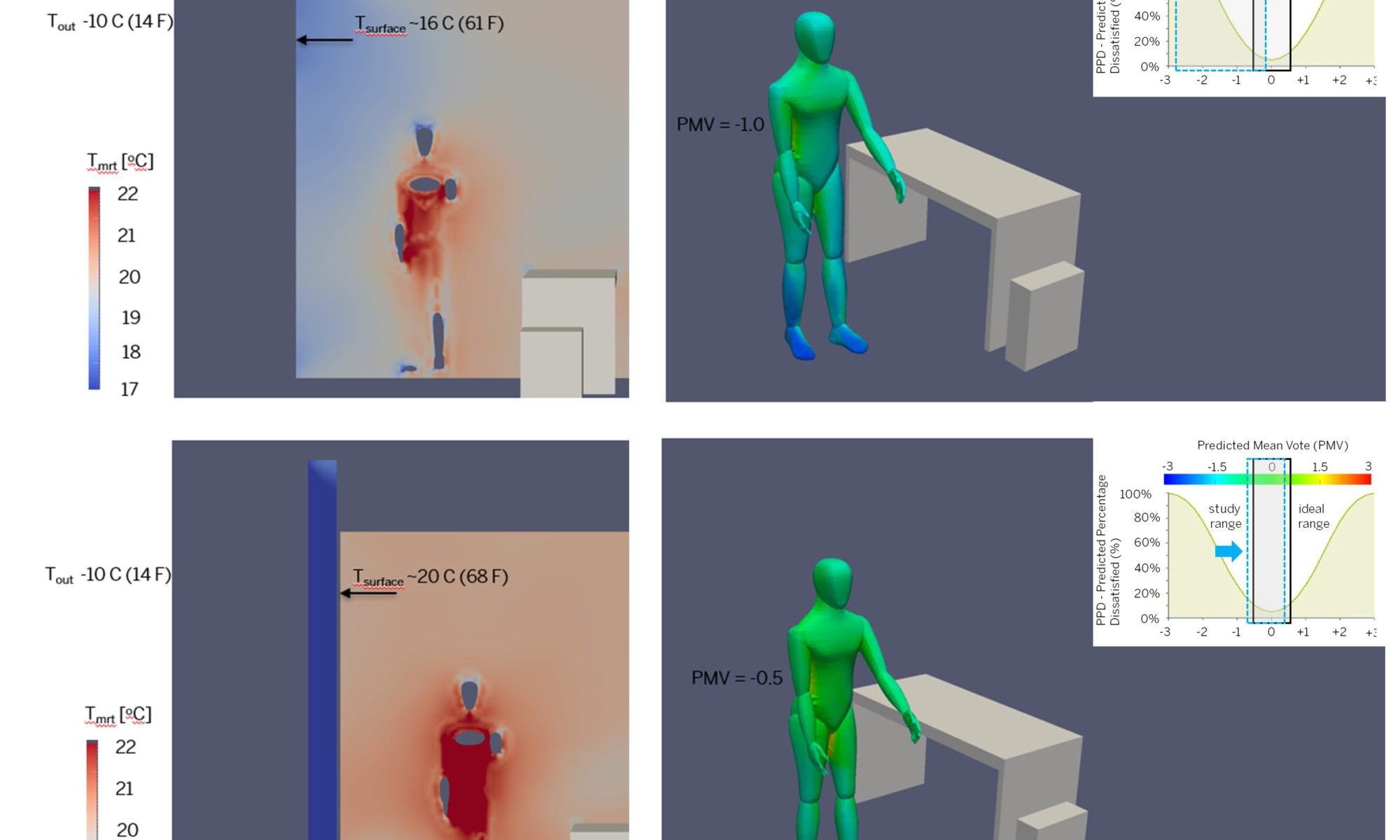
What is the impact of a double cavity wall of an office building on occupant thermal comfort?
Olivier Brouard
Skidmore, Owings, and Merrill LLP
- Olivier Brouard, Sustainability Engineering Team Leader - Stephen Ray, CFD Engineering Specialist
Project Information
Orientation, Location, Weather file, Window-to-wall ratio, Double Glazing, SHGC, Internal heat gains, external solar radiations, HVAC system
Predicted Mean Vote, Mean Radiant Temperature, surface Temperature
2000
5A
- Office
SIMULATION PROCESS SECTION
How is occupant thermal comfort optimized with a ventilated double wall cavity as compared to a double pane insulated glazing unit system?
- Architect - Internal Sustainability Personnel
- EnergyPlus
- Design Development
The tool utilized is not showing in the drop-down menu and is not Energy Plus. Open Foam CFD engine, Helyx gui user interface and Paraview were used to run and visualize the analysis The simulation happened during the end of the DD phase when the design team had to consider double vs triple glazing unit. A double-wall cavity facade was considered to enhance user comfort while reducing energy use through a warm blanket system. The design was integrated collaboratively. Running the timestamp April 26 showing the highest amount of direct beam radiation was used as a worst case scenario. (screenshot below)
The simulation analysis followed the following steps: - highlight the zones of the project - take a typical zoning area and simplify the geometry in rhino - export the rhino model into Helyx - setup the internal, external heat gain from user activity, receptacle, solar radiations, outside and inside temperature, HVAC operative temperature and occupant location neat the perimeter were heat exchanges are the greatest - run open foam computational fluid dynamic software - export results into ParaView to visualize the outputs
The results were visualized over a powerpoint highlighting the major findings
More tools should be listed for Computational Fluid Dynamic software playing a crucial role in transient and steady heat flow condition. Open Foam CFD was used as a back engine, Paraview as a front end interface.